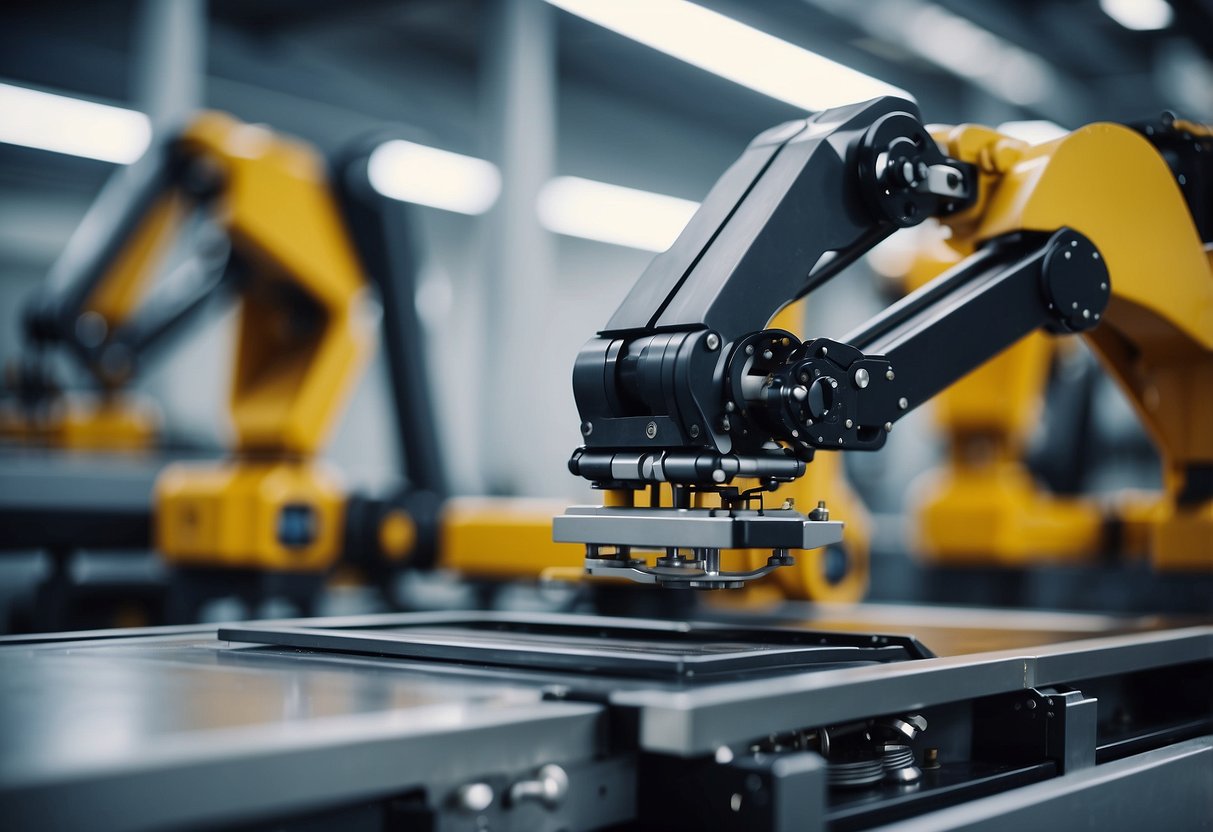
3D Printing Techniques in Car Manufacturing
Different 3D printing techniques bring unique advantages to car manufacturing. Each method varies in terms of materials, precision, and suitability for different components.
Selective Laser Sintering (SLS)
Selective Laser Sintering (SLS) uses a high-powered laser to fuse small particles of polymer powder into a solid structure. This technique is highly valued for its ability to create strong, durable parts with complex geometries. SLS allows automotive manufacturers to produce functional prototypes and end-use parts directly.
Automakers favor SLS for producing lightweight components that can withstand mechanical stresses. The material flexibility offers advantages in creating custom parts. SLS’s ability to print multiple parts at once also enhances efficiency. The technology is commonly used for producing housings, brackets, and intricate parts that would be challenging with traditional methods.
Fused Deposition Modeling (FDM)
Fused Deposition Modeling (FDM) is another popular method in car manufacturing. It involves the extrusion of thermoplastic filaments through a heated nozzle to build layers of material. FDM is appreciated for its affordability and versatility, making it accessible for a broad range of applications.
Car manufacturers often use FDM for prototyping and producing jigs and fixtures. The simplicity of the FDM process allows for quick iteration and testing. FDM is especially useful for creating prototypes that need to test fit and form before moving to more expensive production processes. Materials like ABS and PLA are frequently used due to their strength and ease of use.
Stereolithography (SLA)
Stereolithography (SLA) employs a laser to cure liquid resin into solid parts. It is renowned for its high level of detail and surface finish. SLA is crucial in scenarios where fine details and high precision are required. This technique is commonly used in the automotive industry for creating intricate models and master patterns for molding.
Automotive designers frequently leverage SLA for parts that require a high degree of accuracy, such as interior components or detailed exterior elements. The smooth finish of SLA parts often eliminates the need for additional post-processing, saving time. Resins used in SLA can mimic the properties of end-use materials, making it suitable for functional testing and aesthetic proofs of concept.
Integration of 3D Printing into Supply Chains
3D printing is changing the landscape of car manufacturing supply chains. One primary benefit is the reduction of lead times. Traditional manufacturing methods often require weeks or months for parts to be produced and shipped. With 3D printing, many components can be produced on-demand, significantly speeding up the production process.
Another advantage is cost savings. By printing parts in-house, manufacturers can reduce the need for large inventories of spare parts. This not only lowers storage costs but also minimizes the capital tied up in unsold inventory.
Customization becomes more feasible with 3D printing. Car manufacturers can design and produce bespoke parts tailored for specific models without extensive retooling. This flexibility enhances their ability to respond quickly to market demands and customer preferences.
3D printing also enables the creation of complex geometries that would be challenging or impossible to achieve with traditional manufacturing methods. This opens up new possibilities for innovative design and engineering solutions in the automotive industry.
Quality control improves due to the precision of 3D printing. Consistent, high-quality parts can be produced with less human error involved in the process. This consistency helps maintain the reliability and safety standards expected in car manufacturing.
Supply chain sustainability is another area positively influenced by 3D printing. Reducing the need for shipping parts around the globe decreases the carbon footprint associated with logistics. Additionally, many 3D printing materials are recyclable, contributing to more sustainable production practices.
Overall, integrating 3D printing into supply chains provides numerous benefits for car manufacturers. From cost efficiency and faster production to enhanced customization and sustainability, the impact is substantive. This integration is setting new standards in the industry, offering a glimpse into the future of manufacturing.