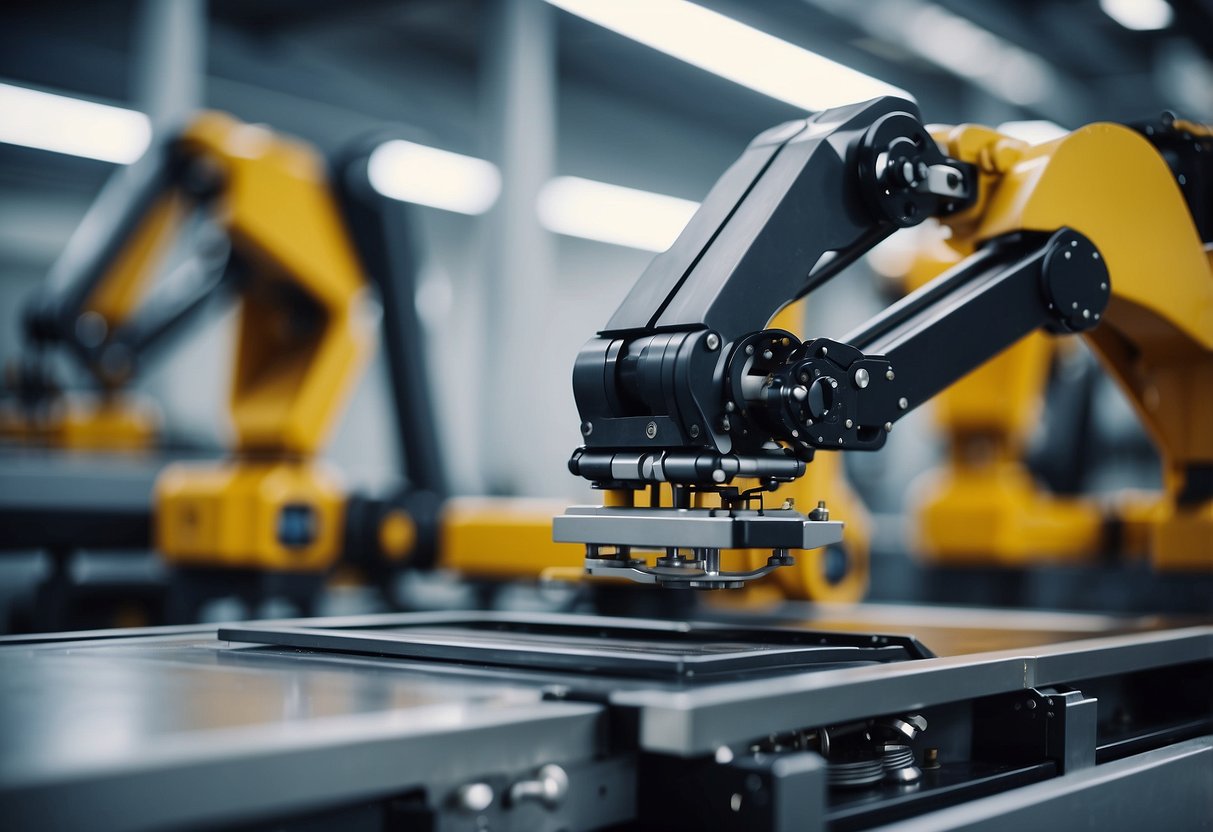
Materials Used in Automotive 3D Printing
Modern automotive 3D printing utilizes a variety of materials, each chosen for their specific properties and benefits. The main categories of materials used are metals, polymers, and composites.
Metals
In automotive 3D printing, metals like aluminum, titanium, and stainless steel are frequently utilized. Aluminum is preferred for its lightweight and strong characteristics, making it ideal for components such as engine parts and aerospace applications. Titanium offers exceptional strength and corrosion resistance, used in areas requiring high durability. Stainless steel, known for its robustness and heat resistance, is often deployed in exhaust systems and structural components.
Metal 3D printing involves techniques like Direct Metal Laser Sintering (DMLS) and Selective Laser Melting (SLM). These methods allow the precise creation of complex geometries, enabling the production of parts that would be challenging or impossible to manufacture using traditional methods.
Polymers
Polymers used in automotive 3D printing include a variety of thermoplastics and thermosets. Materials like ABS, PLA, and nylon are popular choices due to their versatility and ease of printing. ABS is known for its good impact resistance and toughness, making it suitable for interior trim parts and enclosures. PLA is biodegradable and used in less demanding applications.
Nylon offers superior strength and flexibility, often utilized in under-the-hood components requiring wear resistance. Advanced polymers such as PEEK (Polyether Ether Ketone) provide exceptional chemical and thermal resistance, used in high-performance applications.
Composites
Composite materials enhance the properties of base polymers or metals by adding reinforcements like carbon fiber, fiberglass, or Kevlar. Carbon fiber-reinforced composites are prized for their high strength-to-weight ratio, making them suitable for structural and performance-oriented parts.
Glass fiber composites offer good strength and durability at a lower cost than carbon fiber, often used in non-critical components. These composites are typically produced using processes like Fused Deposition Modeling (FDM) or Continuous Fiber Fabrication (CFF), which integrate reinforcing fibers directly during the printing process. This combination enables the production of complex parts with improved mechanical properties.
Advantages of 3D Printing for Car Manufacturing
3D printing offers enhanced customization, reduced waste, and shorter development cycles, dramatically impacting the car manufacturing process.
Customization and Personalization
3D printing allows for unprecedented levels of customization and personalization in car manufacturing. Car makers can create parts tailored to individual customer needs without significant increases in production costs. This flexibility is particularly beneficial for producing limited-edition models or custom parts that would otherwise be economically unfeasible using traditional methods.
Unique interior components, such as bespoke dashboards and customized seating arrangements, can be manufactured quickly and efficiently. The ability to rapidly prototype and iterate design changes based on customer feedback enhances product desirability. This level of personalization not only improves customer satisfaction but also opens new revenue streams for manufacturers.
Reduced Waste and Environmental Impact
3D printing significantly reduces waste in the car manufacturing process. Traditional manufacturing often involves subtractive methods, where material is removed from a larger block, resulting in substantial waste. In contrast, 3D printing is an additive process, which builds parts layer by layer with minimal excess material. This method ensures that almost all the raw material is used.
Reducing material waste has a direct positive impact on both cost efficiency and sustainability. Additionally, 3D printing allows for the use of recyclable materials, further minimizing environmental impact. This eco-friendly approach aligns with the growing demand for greener production practices in the automotive industry.
Shorter Development Cycles
The use of 3D printing in car manufacturing leads to significantly shorter development cycles. Traditional manufacturing methods involve long lead times due to the need for specialized molds and tooling, which can take weeks or even months to produce. With 3D printing, these tools are no longer necessary, enabling faster production of prototypes and final parts.
Engineers can rapidly test and refine designs, accelerating the overall development process. This speed allows for quicker responses to market demands and technological advancements. By reducing time to market, 3D printing gives manufacturers a competitive edge in a fast-paced industry.